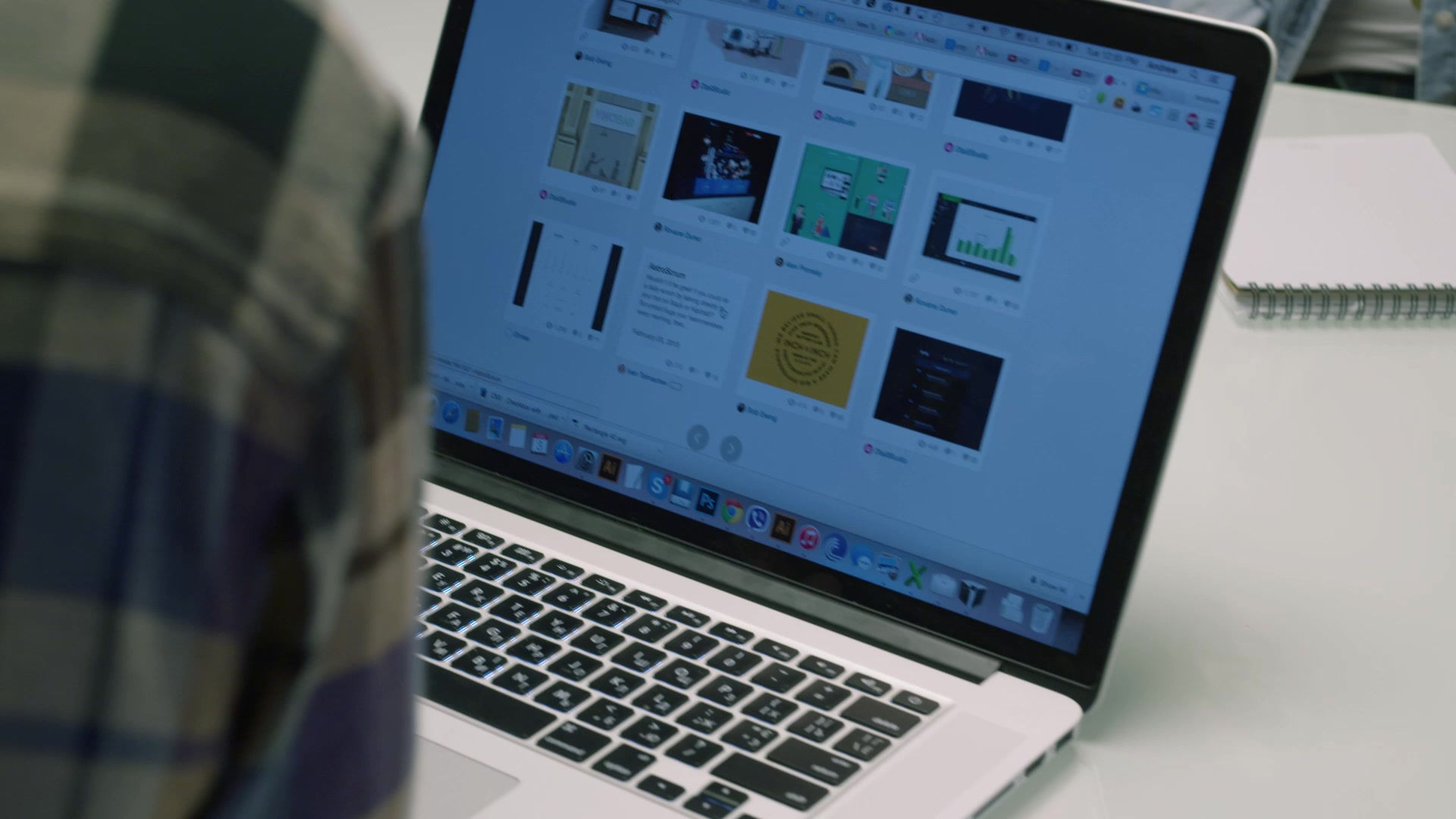
Акселератор Бизнес Решений
Accelerator Business Solutions

Внедрение
бережливого производства
В настоящее время всё большую популярность приобретают различные методы повышения эффективности производства и управления им. Всё больше руководителей различных рангов осознают пользу и необходимость внедрения инструментов и методов «Бережливого производства» (lean).
Бережливое производство (от англ. leanproduction, lean manufacturing) — концепция управления производственным предприятием, основан-ная на постоянном стремлении к устранению всех видов потерь.
Познакомимся с классификацией потерь:
-
перепроизводство считается наиболее вредоносной потерей, так как оно влечёт за собой появление остальных видов потерь;
-
транспортировка, перемещение материалов, изделий, комплектующих;
-
ожидание – простои и бездействие человека;
-
излишняя обработка – видоизменение изделия, придание ему свойств или качеств, в которых не нуждается Заказчик, т.е. за которые он не готов платить;
-
перемещения - когда работник ходит, ценности он не создаёт.
Подходы lean, т.е. правильно применяемые принципы, методы и инструменты, помогают избавляться от потерь как путём непосредствен-ного их выявления и устранения, так и путём создания необходимых культурных и системных условий для их устранения.
Именно в кризисных условиях предприятия, использующие данный подход, получают максимальное преимущество над конкурентами. Компания “Акселератор бизнес решений” поможет вам в достижении этих целей.
Результаты внедрения бережливого производства:
-
возрастает производительность труда;
-
уменьшается время переналадки оборудования;
-
сокращается время производственного цикла;
-
повышается уровень удовлетворенности потребителя;
-
сокращаются объемы незавершенного производства и запасов товарно-материальных ценностей;
-
.увеличивается оборачиваемость денежных средств
Основные аспекты бережливого производства.
Отправная точка бережливого производства - ценность для потребителя. С точки зрения конечного потребителя, продукт (услуга) приобре-тает действительную ценность только в то время, когда происходит непосредственная обработка, изготовление тех элементов. Сердцем бережливого производства является процесс устранения потерь, которые по-японски называются странным для российского слуха словом «муда». Муда - это одно из японских слов, которое означает потери, отходы, то есть любую деятельность, которая потребляет ресурсы, но не создает ценности.
Также принято выделять ещё два источника потерь – мумри и мумра, которые означают соответственно «перегрузку» и «неравномерность»:
Мумра – неравномерность выполнения работы, например, колеблющийся график работ, вызванный не колебаниями спроса конечного потребителя, а скорее особенностями производственной системы, или неравномерный темп работы по выполнению операции, заставляющий операторов сначала спешить, а затем ждать.
Мумри – перегрузка оборудования или операторов, возникающая при работе с большей скоростью или темпом и с большими усилиями в течение долгого периода времени – по сравнению с расчетной нагрузкой (проект, трудовые нормы).
Подходы lean, т.е. правильно применяемые принципы, методы и инструменты, помогают избавляться от потерь как путём непосредствен-ного их выявления и устранения, так и путём создания необходимых культурных и системных условий для их устранения.
Фундаментальный принцип «Ценность – Потеря». Ценность – это то, за что готов платить Заказчик (действия, качества, свойства продук-та и т.п.). Потерями, с точки зрения lean, считаются все действия, потребляющие ресурсы, но не создающие ценности.
Принцип отношений «Заказчик – Поставщик». Работа должна быть направлена на удовлетворение потребностей Заказчика (неважно, внутреннего или внешнего) и создание для него ценности.
Принцип «Line stop» «остановка линии» вариация данного принципа под названием «Quality stop» или «стоп качество». Применяя данный принцип, при обнаружении критических сбойных ситуаций, которые могут заключаться в появлении дефектов, угрозе для безопасности, сбоя в работе оборудования и т.п., работник останавливает свою работу, подаёт соответствующий сигнал и ожидает помощи. Другими словами, работник знает, в какой ситуации он имеет право и должен произвести остановку, он понимает, как он может это сделать, он наделён соответствующими полномочиями. Задача данного принципа – предотвратить распространение проблем при первом их обнаружении, а также перевести наиболее серьезные по степени ущерба виды потерь в наименее вредную из них – ожидание.
Принцип «Go-Look-See» («Иди – Смотри – Увидь»). В основе принципа - непосредственное участие руководителя в решении проблем и реализации улучшений путём следования на место, личного присутствия и обязательного собственного взгляда на проблему или улучшение.
Принцип «принятие решений на основе фактов» является неким продолжением «Go-Look-See», но концентрирует внимание на пре-дотвращении искажения информации при принятии решений за счёт получения её из места создания ценности.
Принцип применения визуализации. Визуализация, т.е. метод представления информации в виде оптического изображения (рисунков, диаграмм, графиков, структурных схем, карт, таблиц и т. д.), является наиболее простым и эффективным способом передачи информации. При помощи визуализации можно не только быстро и доходчиво доводить любую информацию до персонала, но и осуществлять контроль, а также поддерживать уровень информированности на достаточно высоком уровне. Визуализация помогает работнику не забыть доведённую до него и разъяснённую информацию, а также вспомнить её детали.
Принципы целеполагания и планирования. Время реализации стратегических целей и видения организации многократно сокращается при правильной детализации целей и правильном направлении работ персонала. Если каждый работник знает цели организации, понимает личный вклад в их достижение и работает над этим, стратегия реализуется значительно быстрее и эффективнее.
Принцип «командная работа». Работая по отдельности, каждая служба может иметь своё представление о ситуации, возможностях и т.п., но при командной работе видение становится единым, а результат – превосходящим ожидания. Более того, командная работа, например, над какими-либо улучшениями, предполагает присутствие в ней представителя Заказчика, т.е. того, кто непосредственно заинтересован в результатах работ, в результате чего работа движется в нужном направлении.
Основные инструменты lean:
Тайити Оно писал, что производственная система компании Toyota стоит на двух «китах»: системе дзидока и «точно вовремя». Дзидока означает «вытягивание» то есть идею, что последующая производственная стадия запрашивает нужные изделия с предыдущей, а пока этого нет, ничего не производится.
Вытягивающее производство, канбан – продукция «вытягивается» со стороны заказчика, а не «толкается» производителем. Информи-рование предыдущей производственной стадии о том, что нужно начинать работу.
Точно вовремя (Just-in-time) – система синхронизации передачи продукта с одной производственной стадии на другую посредством карто-чек канбан. Комплектующие должны передаваться на следующую стадию только тогда, когда это нужно, и ни минутой раньше.
«Пока – ёкэ» («защита от ошибок», «защита от дурака») – метод предотвращения ошибок – специальное устройство или метод, благода-ря которому дефекты просто не могут появиться.
Кайдзен (kaizen) – непрерывное совершенствование.
Картирование потока создания ценности (КПСЦ) - наиболее распространённый метод выявления потерь в потоке изготовления опреде-лённого продукта. Он является обязательным при выстраивании потока, направлен на минимизацию потерь и улучшение синхронности работы.
Работа по картированию потока создания ценности, как и любая другая, начинается с постановки целей, то есть того, ради чего мы соби-раемся её проводить.
После формулировки целей начинается стадия подготовки. Выполнение работ по достижению целей требует затрат ресурсов и привлечения специалистов на определённое время, это и должно быть предусмотрено на этом этапе.
Этап выбора продукта, по которому будет формироваться КПСЦ, предполагает определение границ рассматриваемого процесса и, в зависи-мости от поставленных целей, расстановку приоритетов среди множества различных видов изделий.
Формирование КПСЦ текущего состояния («как есть») – это более продолжительный этап картирования. Здесь подробно рассматриваются все этапы процесса от входа до выхода, определяются и фиксируются необходимые параметры каждого этапа.
Этап анализа предполагает обработку собранной информации для определения мест воздействия, наиболее влияющих на весь рассматри-ваемый процесс. Основные направления анализа – анализ загрузки этапов процесса (операций) под время такта, анализ проблем потока по степени влияния и потенциалу, анализ качества изготавливаемой продукции, логистический анализ. Этап формирования будущего состояния КПСЦ («как будет») предполагает сопоставление возможностей потока, выявленных в процессе анализа, с необходимыми требованиями к максимальной эффективности процесса.
Разработка плана перехода в целевое состояние – этап пошагового планирования последовательности и сроков реальных действий, необхо-димых для перехода к новому состоянию потока без ущерба для внешнего Заказчика. Предполагается изменение материальных и информационных потоков, физические преобразования, проведение расчётов (количества запасов, времени цикла и т.д.), подготовку к возможным остановкам производства, а также изменение существующей нормативной документации для исключения дублирований или противоречий.
Дальнейшие этапы, например, этап реализации и стабилизации, уже не относятся непосредственно к применению инструмента КПСЦ, т.к. цель картирования как инструмента – это выявление потерь и определение максимально эффективного возможного варианта выстраивания потока. Главное, что необходимо помнить: работа должна быть доведена до конца, план реализации должен являться документом, обязательным к исполнению.
5С. Организация рабочих мест. Это система организации и рационализации рабочих мест, являющаяся аббревиатурой пяти японских слов:
Сэири «сортировка» - разделение вещей на нужные и ненужные и избавление от последних. Предметы (всё, что угодно, начиная с инстру-мента, комплектующих, материалов и заканчивая документацией и личными вещами), которыми не пользовались продолжительное время, удаляются.
Сэитон «соблюдение порядка» - организация хранения необходимых предметов, которая позволяет быстро и просто их найти и использо-вать. Например, то, что используется постоянно, располагается в непосредственной близости. То, что раз в сутки, рядом с рабочим местом. То, что реже, на складе и т.д.
Сэисо «содержание в чистоте» - соблюдение рабочего места в чистоте и опрятности. Рабочее место тщательно убирается и приводится в должное состояние, устраняются источники загрязнения.
Сэикэцу «стандартизация» - необходимое условие для выполнения первых трёх правил. Для предотвращения возврата к первоначально-му состоянию, стандартизируются графики уборки, новое состояние рабочих мест и размещение предметов.
Сицукэ «совершенствование» - воспитание привычки точного выполнения установленных правил, процедур и технологических опера-ций.
5С - это не разовая акция по улучшению рабочих мест, это постоянный процесс их улучшения. Результатом работ должны являться не только чистое, аккуратное рабочее место, но и безопасное и максимально эргономичное.
Всеобщее обслуживание оборудования (ТРМ - Total Productive Maintenance). Классическое представление метода состоит из восьми на-правлений (восьми столбов ТРМ), которые можно перевести следующим образом:
Безопасность. Прежде всего, оборудование должно быть безопасным для работников и окружающей среды.
Автономное обслуживание. Обслуживание и уход за оборудованием самим работниками, обеспечение выполнения простых операций, как при обслуживании собственного автомобиля;
Плановое обслуживание (или профессиональное обслуживание). Сокращение промежутков времени между остановками оборудования и времени аварийных ремонтов;
Обучение персонала. Прививание необходимых привычек по обслуживанию оборудования, проведение обучения и информирования пер-сонала, повышение квалификации;
ТРМ для новых процессов. Встраивание принципов ТРМ в работу нового оборудования, новых материальных потоков или при запуске ново-го продукта. Данное направление также можно назвать ранним предупреждением поломок;
Система обслуживания ориентирована на качество. Разработка мероприятий по встраиванию качества в работу оборудования;ТРМ в офи-сах. Повышение эффективности работы обслуживающих и управленческих подразделений, снижение времени ожидания основного оборудования по данным причинам;
Непрерывное совершенствование. Отдельные улучшения для совершенствования системы обслуживания оборудования;
Быстрая переналадка (SMED - single minute exchange of die). Суть метода заключается в сокращении общего эффективного времени, за-траченного в результате перехода с одной продукции на другую (времени переналадки). Основная цель применения данного инструмента – максимальное снижение размера партии, изготавливаемого между переналадками. Это достигается увеличением количества переналадок за счёт снижения их продолжительности при постоянном доступном для переналадок времени.
Цикличность улучшений. Наиболее известный и применяемый цикл постоянных улучшений – это цикл PDCA или цикл Деминга-Шухарта. В расшифровке цикл PDCA означает планируй (Plan), делай (Do), проверяй (Check), воздействуй или внедряй (Act). Существует ещё один из вариантов цикла, называемый SDCA (стандартизируй, делай, проверяй, воздействуй). Единственное отличие заключается в первой стадии (вместо планируй – стандартизируй). Первый этап этого цикла применяется для неизвестных, нестабильных и не стандартизированных ситуаций. Говоря проще, чтобы что-то улучшить, необходимо понять, что мы улучшаем, поэтому вначале должен появиться стандарт текущей ситуации (как есть). Ситуацию необходимо стабилизировать. Это означает, что мы не должны иметь существенных разбросов в показателях, характеризующих ситуацию, в разные моменты времени. Для этого ситуация должна быть описана в стандарте и отслеживаться.
Анализ внедрения бережливого производства на российских предприятиях
Бережливое производство применяется на российских предприятиях уже много лет. К сожалению, большинство информации об успехах или неудачах в его освоении мы слышим либо из опыта зарубежных компаний, либо от консультантов. Возможно, поэтому бытует мнение, что бережливое производство в России не работает. Но какова же ситуация на российских предприятиях в действительности?
Чтобы выяснить это, провели беседу с представителями тех компаний, которые когда-либо заявляли, что у них применяются бережливые технологии. Информация о применении бережливого производства была получена из открытых источников: сайты компаний, списки участни-ков конференций и семинаров.
Опросить удалось менеджеров девятнадцати российских предприятий. Из них восемь используют подходы бережливого производства, пять применяли, но отказались от дальнейшего внедрения. Представители двух компаний отказались дать информацию о своем предприятии, а один менеджер сказал, что его компания находится в стадии закрытия.
Сначала о тех, кто уже не применяет
Пять компаний из 19 пошли по пути освоения бережливых технологий, но отказались от этой затеи по разным причинам:
-
не получили быстрого обещанного эффекта;
-
не смогли справиться с сопротивлением персонала. Когда работы коснулись конкретных мастеров (рабочих), им не смогли объяснить их личную выгоду и вовлечь в процесс внедрения Бережливого производства, хотя весь управленческий персонал был обучен и полностью вовлечен;
-
не смогли самостоятельно продолжить освоение подхода после внедрения консультантами нескольких проектов на разных участках производства;
-
столкнулись с тем, что за каждым шагом скрывался еще дополнительный не видимый до того объем работ, когда дело дошло до реального внедрения;
-
кризис способствовал остановке преобразований;
-
привычная сложившаяся система управления стала непреодолимым препятствием для нововведений, поэтому предпочли оставить все как есть;
-
у руководства не хватило воли для продолжения работы по внедрения.
Теперь о тех, кто применяет
Из восьми компаний, которые применяют бережливое производство, четыре находятся на начальной стадии. Они внедряют эту систему только последние шесть месяцев. Ситуация у всех примерно одинаковая: на данном этапе управленцы, заинтересованные в освоении подхода, сталкиваются с сопротивлением персонала. Это является их основной головной болью, несмотря на массовое обучение. Сопротивление персонала стопорит весь процесс и о результатах пока речи быть не может.
Две компании применяют бережливое производство в течение трех лет, и запустили некоторые инструменты только в определенных подразделениях. О результатах менеджеры затрудняются говорить или не могут оценить пользу именно от бережливого подхода. Тем не менее, одно предприятие сократило сроки поставки продукции на 40 процентов, другое – сократило время переналадки оборудования с 4 часов до 20 минут.
Еще две компании используют бережливое производство не менее семи лет. Они гордятся своими результатами, не делая из них никакого секрета:
-
производительность труда ежегодно растет на 20-25 процентов;
-
время переналадки оборудования уменьшилось на 100 процентов;
-
время производственного цикла сократилось на 30 процентов;
-
уровень удовлетворенности потребителя повысился на 100 процентов;
-
объемы незавершенного производства и запасов товарно-материальных ценностей ежегодно сокращаются на 10-15 процентов;
-
оборачиваемость денежных средств увеличивается ежегодно на 10-15 процентов;
-
разработана и поддерживается хорошая система мотивации персонала;
-
участвуют во внедрении бережливого производства у своих поставщиков.
Эти компании открыты для общения сегодня, так как на собственном опыте знают, что путь этот не быстрый, и конкурентам вряд ли удастся их догнать. Они уже получили реальный эффект от внедрения бережливого производства, но не собираются останавливаться на достигнутом.
Заключение
Бережливое производство в России работает. Несмотря на значительное число неудач, положительные примеры имеются.
Тем предприятиям, которые пока не смогли получить эффекта, не стоит отказываться от внедрения бережливого производства. Особенно сейчас, в условиях экономического кризиса. Именно в кризисных условиях предприятия, использующие данный подход, получают максимальное преимущество над конкурентами.
Ну а современные подходы, такие, как использование бережливого производства совместно с теорией ограничений, значительно ускоряют процесс внедрения. Быстрое получение результатов снимает сопротивление персонала. У сотрудников появляется мотивация, без которой успех не достижим.
Компания “Акселератор Бизнес Решений” предлагает консалтинг и внедрение «Бережливого производства» на вашем предприятии, мы обладаем необходимыми знаниями и компетенциями.